Winding Film: How COF Properties Affect TNT
- Published: October 18, 2011, By By R. Duane Smith, Davis-Standard Converting Systems
Your ability to apply tension/nip/torque winding principles to produce the desired roll hardness is affected by the film’s layer-to-layer coefficient of friction properties.
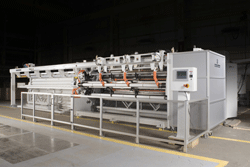
The S4 winder from Davis-Standard Converting Systems.
The goal of every film manufacturer is to wind quality rolls consistently to ensure that their printing and converting customers can produce defect-free products. Roll density or hardness is the key factor for consistently producing quality rolls of film materials.
The amount of inwound tension or residual stress wound into the roll is obtained by using one or more of the TNT. (tension/nip/torque) winding principles. The film’s layer-to-layer coefficient of friction (COF) properties have a major effect on the ability to apply the TNT principles to produce the desired roll hardness without roll defects.
In general, films that have a layer-to-layer COF value of 0.2 to 0.7 will wind well. However, consistently winding defect-free rolls of high-slip or low-slip (low COF or high COF) films usually presents major winding challenges.
Low COF Films
High-slip films have low layer-to-layer COF (generally <0.2). These films often will have inner web slippage or cinching problems when they are winding and/or in subsequent unwinding operations or will have roll handling problems in between these operations. This inner web slippage can result in defects, such as web scratching, dishing, telescoping, and/or starring.
Low COF films need to be wound as tight as possible at the core, usually with high torque, and then taper the winding torque to a minimum amount at three to four times the core outer diameter (O.D.) and build the desired roll hardness using the nip winding principle.
Air is never our friend when winding high-slip films! These films always need to be wound with uniform nip loading to prevent air from entering the roll during the winding process.
The resulting torque of the motor is proportional to the winding tension multiplied by the web width multiplied by the radius of the winding roll multiplied by the taper set by the operator.
For constant tension winding, the torque increases proportional to the radius roll. For constant torque winding, the torque stays constant throughout the winding cycle, and the inwound tension decreases proportional to the roll radius. Normally rolls are wound somewhere in between the constant tension and constant torque winding to achieve the proper roll hardness taper.
High COF Films
Low-slip films have high layer-to-layer COF (generally <0.7). These films often will have blocking and/or wrinkling problems.
When surface winding these high COF films, out of round rolls can be expected at low winding speeds and roll bouncing also can be a problem when winding at higher speeds.
As explained by well-known consultant and PFFC’s "Web Lines" (http://pffc-online.com/web-lines/) columnist Tim Walker of TJWalker+Assoc., (http://www.webhandling.com) "This is due to the fact that the outer layers of a winding roll require a small amount of sliding action as the layers first enter the winding roll. This sliding action produces inwound tension as the air following the web is ejected from the nip or out the sides.
"If the full width slides, this is not a problem. But, if one lane or spot sticks and the rest slide, then a local shear stress will develop near the sticking point. This local shear may form a small buckle or soft wrinkle in the top layer.
"In some products, a small bump or ripple can be wound over and ignored, but in other products (especially optically clear films), the next layer will not smoothly wind over a bump or ripple, but will instead conform over the bump, producing a slightly larger bump or ripple. As additional layers are added, like a rolling snow ball, the defect will often get bigger with each turn." These defects are commonly called slip knots or slip wrinkles.
High COF films are best gap wound with a minimum gap between the following roll and the winding roll. Spreading needs to be provided as close to the winding point as possible. A FlexSpreader covering on the following roll has proven to be successful on a number of high COF winding applications.
R. Duane Smith is product manager of specialty winding at Davis-Standard Converting Systems/Black Clawson Converting Machinery (http://www.bc-egan.com ) group, Fulton, NY. He has been associated with Black Clawson for more than 38 years. Contact him at smithd@bc-egan.com.