Printing Proofs-Color Control: Spot On!
- Published: May 01, 2011, By Edited by Claudia Hine, Managing Editor
Consistent, accurate digital color proofing for the flexographic and packaging markets often is tricky, given the variety of substrates and structural designs that are in play. Add to the mix customers' demands for spot-on color matching and getting products to market at lightning speeds, and you've got the Herculean feats packagers perform on a daily basis.
Industry leader Jones Packaging met its proofing challenges head-on with the installation of GMG FlexoProof color management software, an Epson 9900 inkjet printer, and an X-Rite SpectroProofer spectrophotometer.
The new proofing system, installed by systems integrator Sonor Graphics in June 2010, is right on target, not only cutting time to market, but giving Jones Packaging — and its customers — total confidence in the color proof, all the while slashing material costs by 50%.
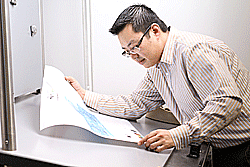
When Jones first started looking for a digital proofing system, “way back when,” notes James Lee, manager of technical services, “there was only one proprietary color proofing system for four-color plus spot colors in the packaging game. It required expensive capital, expensive labor, and expensive material, so it wasn't feasible to buy that system. Instead we outsourced proofs to a service bureau, still paying a lot for these proofs.
“Our service bureau had fingerprinted our presses, but they couldn't calibrate for all the press conditions. While the system was generally very good, we were still having color issues, specifically how the proof was calibrated and how dot gain was simulated. Also, the cost of the proof had to be passed onto the customer.”
Lee and his team looked at different continuous tone proofing options, scouting industry reports and shootouts. “For the most part, systems focused on four-color process and commercial printing, not packaging,” says Lee. “The combination of the Epson 9900, X-Rite spectrophotometer unit, and GMG FlexoProof was the best in terms of color gamut and accurate control of spot colors.”
The system proved its worth almost the moment it was installed. “When we first got it, we put it together and ran a standard out-of-the-box proof set for the SWOP standard. We were amazed at the match — without even any tweaking,” says Lee. “We thought, ‘These guys are good.’”
An Industry Leader
Founded 115 years ago, Jones Packaging produces folding cartons, blister cards, pressure-sensitive labels, full body shrink sleeves, and leaflets for the pharmaceutical and personal care markets out of two facilities in Ontario — one in London and one in Guelph. “We also do a small mix of confectionary,” explains Lee. “The carton size is the same, so it fits our machine capabilities. Plus, we can transfer what we learn from health and beauty and pharmaceuticals and swap that expertise into the other areas — it's allowing us to diversify, too.”
The company, now in its fourth generation of family ownership, certainly has made its mark in pharmaceutical packaging. Its innovative structural designs, including the development of the Medi-Pack compliance blister pack, helped move the converter into a leadership role in pharmaceutical dispensing packaging in Canada, Italy, Spain, and the UK.
The company's mantra — Thinking Ahead of the Box — describes its passion for innovation. Jones offers customers a spectrum of services, from graphics and structure using EskoArtwork software through to fulfillment.
A complement of offset and narrow web flexo presses meets Jones Packaging's varied customer requirements. Four 40-in. sheetfed offset presses include three six-color presses and a specially built 13-unit Komori, configured with nine print units, two flexo anilox coating stations in front and back, ultraviolet (UV) extended delivery unit, and two infrared drying stations. Jones is able to run white or metallic colors in front and varnish coating on the back end.
The company's stable of presses also includes three Sanjo rotary letterpresses for commodity labeling and two Comco presses used for shrink sleeve film, carton board, and flexible packaging films. A nine-unit Gallus EM 280 UV flexo label press delivers high-end labeling for the pharmaceutical and health and beauty markets and also is used for jobs requiring silkscreen, hot/cold foil, and embossing.
Confidence Booster
From the get-go, the GMG proofing system has had an impact on workflow at Jones Packaging. Costs and time to market have been shaved significantly. “With the proofing system that our service bureau used, we were paying by color,” says Lee. “The size of the page is just a start. Every color adds a cost. Bringing proofing in-house, we have saved more than 50 percent of material costs on each proof.”
Deliveries to and from the service bureau are no longer costing time, and the proofing cycle time — due to the system's capabilities — also has been shortened substantially. “Cutting as much internal time was essential, because there are such tight ‘time to market’ demands,” Lee says.
Jones recently took a job rebranding an over-the-counter drug with 16 SKUs. “Because we were able to accurately load spot profiles easily, and then ‘proof, proof, proof, proof,’ it offered a faster speed-to-market than if we had to farm out 32 proofs to our service bureau,” says Lee.
“It would have been more expensive, and it would've taken a couple days. We were able to get the entire job finished in three hours. Also, since each file had the same setup for proofing, we could gang proofs with 42-inch media from GMG. We had a giant sheet with all these SKUs and just one color bar. It was a resounding success in terms of the sheer volume we output within a compressed time period.”
Jones Packaging is so confident in its GMG proof, “we are using it as an investigative tool,” says Lee. “A lot of customers don't provide press targets. If something goes weird on press, we rely on the characterizations we developed using FlexoProof to help with issues. We create a proof and see where a color is out of whack. We can even verify a blanket change internally.”
This capability came in handy for a recent job for a large national brand. “There were problems with one of the SKUs compared with all the others in the family. We found out there was excessive dot gain in one station,” explains Lee. “The press operators were blaming the file, saying there was something wrong with it. We used FlexoProof to show what happened.
“We took the characterization data and bumped the gain. When we ran the proof, it matched what we had on the press sheet. We showed the pressman a good proof, then the one with the gain. The pressman admitted that we were right. There was a 35 percent dot gain on magenta caused by a worn printing blanket.”
Color Control
A key component of GMG FlexoProof is its ability to provide specific control over ink curves for spot colors, delivering an accurate rendition at specific screen percentages. “Because FlexoProof provides stability for gradation curves, we are in control of spot colors,” says Lee.
Data on the spot colors show how colors let down. “When I print on a press, the color shifts differently when running 100 percent of a 485 red or when I am running 40 percent of a 485,” notes Lee. “The ink supplier, the pigment, or whether it's UV or conventional can all impact color shifting. With FlexoProof you can program those shifting differences, giving you control of those spot colors.”
FlexoProof, says Lee, makes finding out what went wrong very easy. “In the past, it would have been tougher with ProfileMaker and ICC profiles. Now we just slap a curve on it — like we did with the magenta dot gain — and find out what went wrong.”
The X-Rite SpectroProofer and GMG ProofControl flag defects in the proof. The SpectroProofer sits outside the Epson device, reading color bars as they exit the printer. It is easy to install and use, says Lee, integrated with GMG's ProofControl to ensure that a proof is within accepted calibration settings.
If everything is good to go, a label is printed approving the proof and showing the Delta-E. If not, a failure sticker is printed. Proofing software can be programmed to run calibration tests at a specified time, automatically recalibrating the device if it is outside of specifications.
Looking ahead, Lee expects to expand the FlexoProof system's role in the prepress workflow, further integrating the software with EskoArtwork technology and using the DotProof module for halftone proofing. Jones can use FlexoProof to simulate the texture of substrates used during the press run, as well as replicate the press's dot gain and shifts in registration. For now, Lee and company are reveling in the knowledge that “we have the best system for the packaging market and the confidence that our proofs will make the grade.”
Converter Info
- Jones Packaging | 3000 Page St., London, ON N5V 5H3 Canada | 519-451-2100 | www.jonespackaging.com
Supplier Info
- GMG | www.gmgcolor.com
- Epson America | www.epson.com
- X-Rite Inc. | www.xrite.com
- Sonor Graphics | www.sonorgraphics.com
- EskoArtwork | www.esko.com
- Komori Corp. | www.komori.com
- Sanjo | www.sanjo-kogyokai.or.jp
- Comco | www.markandy.com
- Gallus | www.gallus-group.com