Wen Chyuan Brings Western Quality to Sheet Fed Lamination
- Published: April 20, 2020
Submitted by Vetaphone
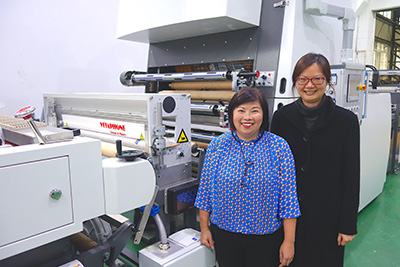
Established in 1972 by engineer Lin Chi-I, Wen Chyuan Machinery Company has become one of the leading manufacturers of sheet fed varnishing, laminating and converting equipment in Asia, with strong sales in China, the Middle East and increasingly Europe and America. From its headquarters in New Taipei City, Taiwan, where it employs more than 40 people on manufacturing, assembly, sales and administration, with an additional 40 in China who concentrate on service, the company has always prided itself on innovation and investment in the latest technology to guarantee performance.
Sales Director Emma Lin takes up the story: “We keep a close eye on market trends and work hard in R&D to ensure that our technology meets and exceeds our customers’ requirements. This is not a cheap process as it involves using the highest quality components, but it’s what our customers expect from us, and is justified by the high level of repeat business we enjoy.” Lin, along with second generation family members Kevin (managing director), Bob (director of R&D) and Amber (marketing manager), are all committed to the business and know how important teamwork is for a successful company.
One of the key elements of business at Wen Chyuan is quality control, and with a healthy export market and eyes on growing its business in Europe and the USA, the company knows it needs to work with companies that are CE and UL approved. And, it was one such conversation with local Vetaphone agent Carol Liang that led to beginning of what has grown into a flourishing partnership between the two.
“We had previously used corona systems manufactured in Asia but found them to be unreliable and inconsistent in the dyne level they could deliver,” said Lin. “This lack of quality was reflecting badly on us with our customers who demand top quality every time.”
Following detailed technical discussions with Vetaphone at their HQ in Denmark, an agreement was reached to install a test machine at Wen Chyuan’s plant to allow customers to see for themselves the difference that quality corona treatment makes, and also to test new jobs on different substrates. It proved an overnight success, as Emma Lin explained: “Although more expensive initially, the Vetaphone corona systems have a far lower total cost of ownership, and most importantly showed an immediate improvement in lamination quality that impressed our customers. We laminate a lot of metallised and clear film to board for subsequent printing, so quality control of the process is essential – Vetaphone units give us that guarantee.”
The most popular of Wen Chyuan’s laminators is the KYE-108DRK model, which features a dual-set dust remover, a glue coater, dryer and laminator, with a disc knife or flying knife cutter. It is designed for water-based adhesive lamination that makes it environmentally friendly and offers thermal lamination as an alternative function. Sheet overlap is controlled and adjusted by a servo motor for accuracy and the dust remover lifts all printing powder from the wet ink. The 300mm laminating roller and 800mm drying roller are both fed by hot water in a re-circulating system that is temperature controlled, while the hot-air dryer consumes 20 percent less power by re-circulation. Available with a disc knife for BOPP film or a flying knife for BOPP/PET/metallised film, the machine comes in three sizes from 910 x 1080mm maximum sheet size up to 1450 x 1080mm, and will handle stocks from 100 to 500gsm at speeds up to 70m/min.
Currently, Wen Chyuan and Vetaphone technicians are working on a new project that will add a second corona treater prior to the coating station to help boost the dyne level on pre-treated film, with Wen Chyuan developing a double-sided laminator/embosser.
“As the brand owners demand greater shelf-appeal for their products, converters need to add more value to the packaging. You can only do this if the production process is of the highest quality, and in many cases it’s the ancillary items that are the weakest link in the chain. Now we are working in partnership with Vetaphone we can confidently tick one of those boxes safe in the knowledge that quality is assured.”
“We are delighted to have struck up a working relationship with Wen Chyuan because we see a real synergy between our two companies, both of which focus on bringing consistency and reliability to our mutual customers,” said Vetaphone’s Vice President of Technical Sales, Kevin McKell. “In the highly competitive market for value added packaging, quality engineering will always win out, and we are looking forward to working closely with Wen Chyuan on a variety of new projects in the future.”