Wet on Wet
- Published: October 01, 2007, By By Edward Boyle, Contributing Editor
EB Flexo
The industry’s increased focus on sustainable development encourages the business community to bring an environmentally conscious, life-cycle approach to all aspects of its businesses. Many converters have found that good citizenship and good business are not mutually exclusive.
For example, Uniprint Knauer (formerly UV-Flex) recently installed a Fischer & Krecke WetFlex ten-color Flexpress 16 S press. It features Sun Chemical’s WetFlex technology, Energy Sciences’ EZCure-I electron beam (EB) curing system, and Advanced Vision Technology’s PrintVision/Argus defect detection system.
The flexographic printing process applies Sun Chemical’s UniQure inks wet-on-wet to the substrate; the inks are in-line EB cured, thereby reducing energy costs and improving quality, according to Uniprint managing director Rainer Schroepfer.
The press also offers “dramatically reduced” changeovers and subsequent labor cost reductions, greater standardization, increased register accuracy and impression precision, and “perfect repeatability,” says Schroepfer.
Setting New Standards
The press has a print width of 53 in. (1,350 mm) and repeat lengths of 12.6-41 in. (320-1,050 mm). It has a mechanical speed rating of 2,000 fpm, though actual line speed is determined by the inks. The in-line laminating process, where EB-cured adhesives are applied at the press, contributes to the efficiency of the line, says Schroepfer.
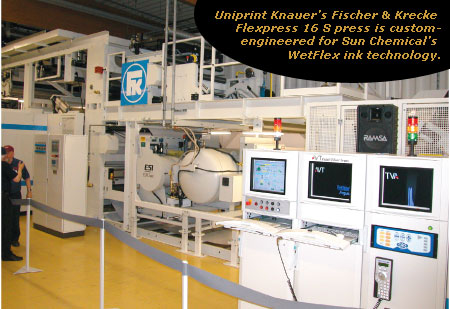
With the installation, to be used mostly for printing foils, plastic film, and laminates for lidding of containers for food and dairy markets, the converter is setting what it calls “new standards” for print quality, production efficiency, and environmental responsibility.
“Any new technology that can deliver all those benefits will significantly impact the industry,” says Schroepfer. “UniPrint is able to provide an absolutely safe packaging material—no solvent remainders, no remainders of photo initiators. It was clear that with the right equipment, this process could allow us to print faster, more efficiently and cleanly, and more brilliantly.”
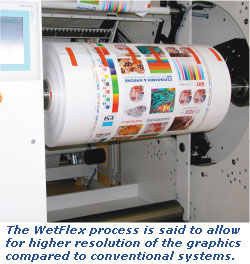
Schroepfer notes WetFlex also is ideally suited for an expanded gamut printing process—using five, six, seven, or more standardized colors. He claims this standardization provides enhanced print quality and reproducibility of print jobs, as well as a further significant reduction of changeover times due to eliminating washups and the elimination of leftover ink.
“We believe WetFlex will become a widely used flexo process because it has so many advantages, not only because of the quality aspects but also because of the environmental friendliness,” says Schroepfer. “All industries have to take responsibility for reducing CO2 emission. With the WetFlex process, you get the same output for less input of energy.”
The WetFlex process and the F&K press allow for a much higher resolution of the graphics compared to conventional systems that use solvent- or water-based inks, says Schroepfer. This is due to a finer line screen (up to 80 l/cm) and higher color strength of the inks, finer aniloxes, and a more homogeneous dot structure. In addition to the high resolution capability, he further explains, the excellent trapping behavior, the density stability, and the brilliance and durability of the WetFlex inks ensure high quality flexo printing graphics.
The press uses what ESI calls “revolutionary” technology that allows flexo inks to track through the press without smearing during wet-on-wet applications. Consequently, ultimate drying is critical.
Advancing the Process
Schroepfer says he first became interested in UV technology in 1995 when he founded UV-Flex and installed his first UV press. A second was brought on-line in 1999 and a third in 2003. His first encounter with WetFlex came in 2005 on a visit to Sun Chemical for information on the latest technology.
Convinced that WetFlex offered too many benefits to be ignored, UV-Flex began the search for equipment that could advance the process to a commercially viable installation. After speaking with several manufacturers and looking at a demo of a European central impression (CI) flexo press modified to accommodate the WetFlex process, Schroepfer decided that a high quality CI flexo press offered the best match for Sun’s new technology. He felt that only a rigidly constructed, high-end press engineered specifically for the WetFlex process would achieve the company’s goals.
“Of two well known, high quality press manufacturers that made the final cut to serious consideration, it became clear that Fischer & Krecke was the best choice for us,” says Schroepfer. “They were as excited as we were about the project and well positioned to produce a custom-engineered press and provide across-the-board support.”
And that, he suspects, will help sustain the company’s own development for years to come.
Open House Draws International Attention
After taking delivery of Fischer & Krecke’s first CI flexo press designed for Sun Chemical’s WetFlex technology, Uniprint was happy to show it off. So the company held an open house April 18-19 at its facility in picturesque southern Germany.
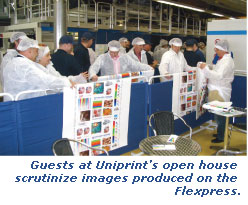
The gala event drew 260 international guests eager to examine the high-grade print produced on the press. Guests also heard presentations by representatives from F&K, Sun Chemical, and Energy Sciences.
Says Rainer Schroepfer, Uniprint Knauer managing director, “We were delighted to welcome so many knowledgeable and distinguished guests to our facility and to present our WetFlex line, which performed flawlessly.” Regarding the suppliers that worked on the project, he adds, “Without these extraordinarily knowledgeable partners, we would not be where we are after only a few weeks of intense testing work.”
For more on WetFlex, see our March issue p24 or click here.
SUPPLIER INFO:
- Fischer & Krecke | fischer-krecke.de | PFFC-ASAP 308
- Sun Chemical | sunchemical.com | PFFC-ASAP 309
- Energy Sciences | ebeam.com | PFFC-ASAP 310
- Advanced Vision Technology | avt-inc.com | PFFC-ASAP 311