From Pouch to Pooch
- Published: July 01, 2007, By Edited by Claudia Hine, Managing Editor
Flexible Packaging
WetBone Co., Kensington, CT, has launched a bone-shaped pouch with a reservoir for purified, vitamin-enriched water at the bottom and a drinking bowl at the top. The pouch, a three-layer, polyester/foil/linear low-density polyethylene (PE) lamination, is being manufactured by the Ampac Flexibles business unit of Ampac Packaging.
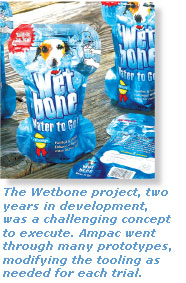
Wetbone’s patent-pending delivery system relies on an additional 4-mil piece of PE (an upside-down gusset), the middle section of which is heat-sealed to opposing inner walls of the flexible pouch (close to the top) to create a hammock-like drinking bowl. Four voids in the heat seal (two on each side) create small 9-mm channels that enable the water to transfer from the lower compartment into the top section when the pouch is squeezed.
To use, the pet owner simply removes the tear strip at the top of the flexible “bone” and opens the press-to-close zipper. Then one hand is used to squeeze the bottom of the pouch, while the other is cupped around the top section forming a rounded opening. The squeezing action forces water through the channels and into the bowl area for the pet to drink.
The channels allow the water to trickle back down into the bottom receptacle if the dog doesn’t drink all of the liquid. The press-to-close zipper enables the pouch to be resealed for later use.
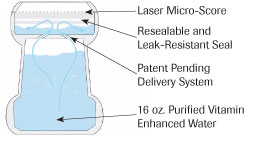
Channel System Challenges
According to product developer and Wetbone cofounder Sue Tyska, “The most challenging part was the flow rate. We didn’t want a ton of water in the bowl when the consumer first opened the pouch. We needed to find a way to properly move the water from the reservoir into the bowl and do it in a way that would give us a pouch that could be commercially manufactured in a cost-effective way.”
Some of the challenges included a structure that was thick enough to enable the pouch to stand up and to survive drop tests, while still being cost effective. The real “magic,” however, was modifying the automatic heat sealer to create appropriately sized gaps in the seal so the channels were formed.
Steve Herlehy, account representative at Ampac, explains, “You need to create a channel system that allows water to migrate into the upper bowl—not too slow and not too fast. We were shooting for a filling speed of five to seven seconds when steady pressure is applied to the bottom reservoir.”
Ampac engineers had to modify the sealing jaws to make sure exactly the right amount of heat was present so the channels didn’t inadvertently seal shut as a result of radiant heat migrating from the contact points. Creating the channel at an optimum angle for filling was also an issue. The location of the seal placement and size of bowl were additional considerations.
“We selected 16 ounces because you want to have an amount that isn’t going to disappear in one serving. We also didn’t want to go too big, because we still needed the pouch to be portable and to also fit into a pocket or bag,” Tyska says.
“My partner and cofounder Tony Tropea is the genius behind the graphic and package design,” Tyska says. “He took advantage of the five-color rotogravure printing process as well as the foil material. The result was a product that screams off the shelf and establishes a strong brand identity.”
CONVERTER INFO:
Ampac Flexibles
12025 Tricon Rd.
Cincinnati, OH 45246
513/671-1777; ampaconline.com