The Case for Air Cylinder Standardization
- Published: October 01, 2007, By By Klemens Ehrlitzer
October 2007 Web Exclusive
In an industrywide initiative during the summer of 2006, various sleeve manufacturers joined forces under the umbrella organization of the German-Speaking Flexoprinting Section (DFTA) to achieve a standardization of air cylinders. What has become of this project?
During the recent DFTA Spring Conference, held March 27–28, 2007, in Kassel, Germany, Heinz W. Lorig and Mario Busshoff, the managing directors of Polywest Kunststofftechnik and Rotec Hülsensysteme respectively, offered their opinions.
Both sleeve manufacturers see the standardization of air cylinders as an important contribution to the further development of flexographic printing that will bring advantages all round. They both back the recommendations expressed at the meeting of the international sleeve industry in the DFTA offices last year. Apart from Polywest and Rotec, this meeting also was attended by the AKL, DuPont, Inometa, MacDermid, and Rossini.
The quality criteria and tolerances for a total of ten design parameters are specified in the standardization recommendations. These relate to the surface quality, shape, and diameter of the air cylinder, as well as size and positioning of outlet openings to guide the compressed air. The fixed standards are not simply randomly chosen parameters. They are based on the Stork system that has been in use for many years and is widespread in the industry.
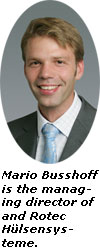
Aimed at New Equipment
As Busshoff explains, the standardization primarily is aimed at new equipment for printing presses. The fact that current flexo presses are fitted with air cylinders that differ in many respects from the recommended standard is, at present, causing some very high costs. The additional expenses are due, for example, to the fact that in these cases the sleeves generally are very costly, customized solutions.
Lorig, too, is convinced that a standard for air cylinders will reduce today's expenses significantly and work in terms of investment costs, order settlement, administration, custom-made products, etc., in the procurement of sleeves. A sideways glance at other industries shows just how necessary standardization is.
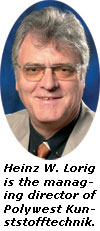
Lorig compares the complete system for a flexo printing form, often consisting of air cylinder, adapter, and sleeve in modern central cylinder machines, with wheels in the automotive sector, which also are made up of the components axle, rim, and tire. A standardization for this automotive industry example is understandable to anyone. Analogous to this, quality criteria and set parameters also should apply equally for all individual components for flexo printing forms.
The high demands made on the quality and precision of printing forms and adapter sleeves for today's flexo printing only can lead to the set goal—and this is something on which both Lorig and Busshoff agree—if the dimensional accuracy and quality of air cylinders also are included in the system. This opinion is shared by the DFTA. After all, the association has been calling for a greater standardization in flexo printing for many years to improve the competitive strength of this printing method. DFTA supports the initiative by publishing the standardization recommendations on the association's website, for example.
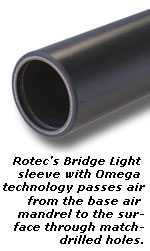
Win-Win Situation
A standardization of air cylinders will bring some lasting advantages for everyone concerned—be these printing shops, sleeve producers, cylinder manufacturers, or the engineering industry. In view of this "win-win situation" neither Lorig nor Busshoff can understand why the initiative that began so promisingly last summer made no further progress in the following months. It is hoped this understanding between two otherwise rival sleeve manufacturers will breathe new life into the standardization initiative, above all for flexo printing shops that invest in the new machine technology.
Whatever the case, Polywest and Rotec are able to exert a noticeable influence over the global flexo printing market. Together they supply the great majority of printing forms and adapter sleeves used worldwide. Users are thus given an important choice: They can order standardized products from more than one manufacturer. In the medium run, this will help accelerate the development of a recognized standard for air cylinders in the flexo printing industry.
Based on former experience, the two sleeve manufacturers already have some far-reaching standardization plans. For example, they are considering the possibility of reducing the great variety of sleeve sizes. The definition of preferred sizes on which practical applications concentrate would open up an as yet untapped potential for cost savings within the flexo printing process chain.
SUPPLIER INFO:
- Polywest Kunststofftechnik | polywest.de
- Rotec Hülsensysteme | rotec-sleeves.com
- AKL Flexo Technik GmbH | storkprints.com
- DuPont Packaging Graphics | dupont.com
- Inometa GmbH | inometa.com
- MacDermid Printing Solutions | macdermid.com
- Rossini | rossini-na.com
- Stork Cellramic | storkanilox.com
-
Klemens Ehrlitzer is a freelance journalist specializing in package and label printing. He has more than 20 years of experience in this business sector. Before founding his editorial office, flexible kommunikation, in Hoechberg, Germany, he was editor and chief editor of several trade magazines. Contact Ehrlitzer at + 49 (0) 9 31-40 51 66; flexible.kommunikation@t-online.de.