Shear Slitting Can Provide Advantages
- Published: July 31, 2004, By Keith Fordham, Ashe Converting Equipment
Shear slitting offers many advantages and can be used in several ways. Each has its merits, so give careful consideration to selecting the best arrangement, as there is no clear-cut winner.
Shear slitting can be likened to using a pair of scissors, except two rotary knives are used. To further our understanding, let’s stay for the moment with scissors.
We’re all familiar with the action whereby the two sharp blades of the scissors cross at an angle and cut. To achieve this, material force is applied on the handle, and as the angle of the junction of the two sharp edges closes up, the cutting takes place.
Now, taking the scissors, hold them open, and push a sheet of paper through. At a certain angle, the blades will cut cleanly; however, alter the angle ever so slightly and the paper tears. This is, in effect, the action that takes place with rotary knives in shear slitting.
Returning to our slitting environment, if the web is running slower than the knives, effectively the knife will close in on the web or cut in the way scissors cut. Conversely, if the web is running faster than the knives, the effect is the same as if we were pushing paper through the scissors. This is why material can be slit effectively at a knife speed that is either slower than synchronous, synchronous with the web, or faster than synchronous. The angle of junction between the knife cutting edges is the critical factor.
With the two rotary knives, let’s visualise two circles that overlap to form a junction angle similar to that formed by the scissors. Squeezing the blades together creates a reaction force, which pushes the blades apart. This is the same force that is used to squeeze the handle of the scissors. When a large number of cuts are being made, these reaction forces can bend a knife shaft. This is a factor that must be considered in all slitting operations. No table for shearing forces required for various materials is yet available.
Generally speaking the effect that the relative speed between the material and the knives has on the shearing force has not been quantified satisfactorily but is being studied. One opinion is that when the knives are running faster the unit shearing force is less. This is because less material is being cut per knife revolution than would be at synchronous speed. This means that at a higher knife speed the shearing forces will be lower.
Also under study is the relationship between knife speed and slit edge quality. There is some indication that faster speeds are better for foil. It should be noted that most plastic films and papers are slit at synchronous speeds and with excellent results. On most materials, problems exist at speeds that are below synchronous.
Next we should consider the configuration of the web and the knives in the machine. There are two primary arrangements—wrap and kiss slitting.
With wrap slitting, the web actually wraps around the female knife and is positively supported while being cut. The arc of contact between the web and the female knife must be greater than the arc of contact between the male knife. If the arc of web contact is smaller than the arc of contact, then the male knife will hit the unsupported section of the web, which will then be torn apart rather than cut. Knives and spacers, therefore, must be assembled on the shaft to form or to simulate a solid supporting shaft. Unless the web is supported, it will pull or sag into the voids and lead to irregular slit widths.
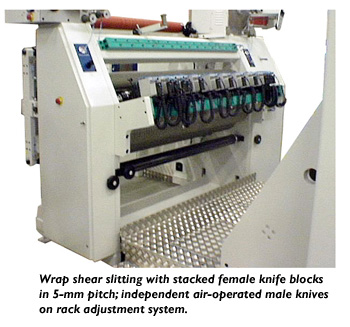
In wrap slitting, it’s possible to achieve highly accurate slit widths and close tolerances through the use of spacers for measuring and positioning the knives. This combination of knives and spacers, stacked on the shaft, provide a complete support for the web, thereby reducing to a minimum the possibility of wrinkling, bagging, or sagging.
In tangential or kiss slitting, the web only touches the outside diameter of the female knife, it doesn’t wrap around it. Should the web hit the male knife before it hits the female knife, a cutting angle is not achieved and the web is ruptured not cut—in effect much like taking a pair of scissors and trying to cut with only one blade. Again, if the web hits the female knife first, nothing happens, but when it leaves the female and then hits the male, the web also will be ruptured and not cut cleanly.
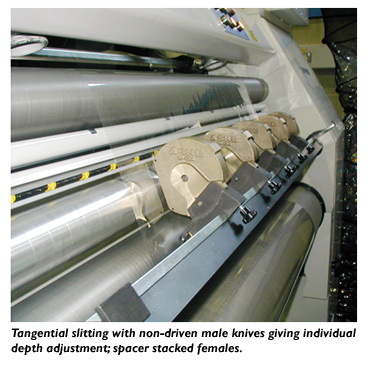
It is therefore essential that both the female and male knives make contact together at the critical point. This critical point is subject to change as the male knife overlap is increased. It therefore means that beyond a certain point any overlap will cause problems. The ideal condition is minimum overlap and point contact (kiss).
Increasing overlap increases the arc of contact between the two knives and the male knife hits the web before the female. Using a smaller diameter male knife will give a greater overlap prior to reaching the critical point. Conversely, the greater the diameter of the male knife, the smaller permissible overlap. The use of individual knives, permitting fine adjustment, provides greater control than using multiple knives mounted on a single shaft where accumulative tolerances must be overcome by increasing overlap.
The main advantage of kiss slitting is that the individual female knives can be set up quickly. These knives can be repositioned on the shaft without removing the entire knife shaft. Wrap slitting, on the other hand, necessitates the removal of the shaft from the machine, taking off both the knives and spacers and then putting them back in a rearranged order.
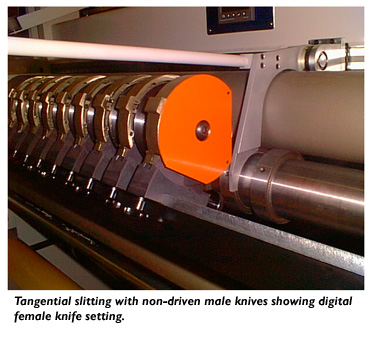
In kiss slitting the cut is not as good as with the wrap method. In wrap slitting, the web wraps around the female knife and the male knife penetrates to the ideal depth and gives a good clean cut.
In conclusion, shear slitting offers many advantages and can be used in several ways. Careful consideration must be given to the desired results or in selecting the best arrangement. Irrespective of selection, it’s standard practice to incorporate driven rolls in all types of machines to maintain control of the web as it passes through the knives and to isolate the slitting tension from the unwind and rewind tensions. All driven rolls also serve to keep a constant tension in the slitting area, thereby maintaining the slit width.
A slight overdrive in web speed is maintained from driven roll to driven roll to hold tension constant. For speeds in excess of 500 fpm and for ultra-thin films, it is necessary to positively drive all rolls since changes in web speed, due to undriven roll inertias, will tend to distort the web and affect the quality of the rewound rolls. This is particularly true when narrow webs of light plastic films are run on wide machines.
There is no clear-cut winner when it comes to choosing the best possible slitting solution; each has its merits and disadvantages.
Keith Fordham is chief engineer at Ashe Converting Equipment, Ipswich, Suffolk, England. For more information, contact the author by e-mail at Keith.Fordham@ashe.co.uk or visit ashe.co.uk.