If Not Rough, How About Groovy?
- Published: February 28, 2006, By Timothy J. Walker, TJWalker & Assoc. Inc.
Web Lines
Last month I presented the cases for rough over smooth in preventing slip and scratching problems (see "Are You Rough Enough?"). Even though rough surfaces have a bad reputation, rough is better than smooth to fight lubrication from air or liquid lubrication. But is rough the best solution?
Creating a rougher roller surface from machining or bead blasting is effective and inexpensive, but rough surfaces do have drawbacks. Rough surfaces can prove difficult to clean, both from snagging your cleaning cloths and collecting crud in their deeper valleys. The reduced contact area can be good for release properties but bad for heat transfer. The machined and blasted rough surface profiles get much of their peak-to-valley difference from a limited number of peaks. Even a small amount of wear or applying a thin, hard coat will reduce their Ra and lubrication-preventing powers significantly. Creating a specific Ra value from machining or blasting may be difficult to repeat from lot to lot or supplier to supplier.
So, how else can you fight an air or liquid lubrication beside simple roughening techniques? For a quick change in roller roughness, try a roller wrap. By far the most popular choice is masking tape. Masking tape is inexpensive, has a low tack adhesive that is removed easily (if you don’t leave it exposed to UV light too long or bake it on), and it conforms easily to the roller’s surface. Masking tape also creates two levels of roughness from both the tape roughness and the ridges or grooves of the tape thickness.
Other popular choices for roller wraps include fabrics (including cheesecloth and sailcloth); netting (including pantyhose); abrasive tapes (such as emery cloth or safety walk tread); cork; and embossed rubber tape.
Roller wraps have some drawbacks. They can wear or fall off, sending bits of debris out the door with your product. Wraps may insulate any desired heat transfer or create more (or less) electrostatic charging or dissipation. Acknowledging these drawbacks, roller wraps remain a quick, inexpensive solution.
For a long-term solution with consistent performance, add grooves or ridges to your roller. Ridges and grooves are cut into your roller materials, whether steel, aluminum, or rubber, and can be hard-coated without changing their performance significantly.
Any grooved or ridged surface is defined by four variables: pitch, depth, width, and angle. Whether a cut pattern is a groove or a ridge depends on what percentage of the surface is raised or recessed. Grooved surfaces are far more common, since a web can span a small gap without much deflection, but even the narrowest ridge can wrinkle a thin web.
To prevent lubrication, I look for a fine groove pattern, with a 10–20 pitch (grooves per inch). I’ve found at this pitch, a groove depth of 5 mils/in. of radius (same for groove depth) works to prevent air lubrication in even extremely high speed-to-tension ratios. I’ve seen rollers with big grooves and small pitch. The big grooves seem more than adequate to channel away unwanted air, but the distance between grooves, even at 1 in., is too far for air to travel in the short contact time on the roller, reducing the expected benefit.
What groove angle is best? Axial grooves can be noisy; annular hoop grooves may catch and hold wrinkles. Chevron pattern grooves are a good choice, and diamond patterns are the most popular.
Consider a car tire. Grooving or tread, not roughness, is the engineered solution to prevent lubrication. Grooved rollers are also a well-engineered solution.
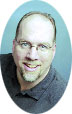
Timothy J. Walker has 20+ years of experience in web handling processes. He specializes in web handling education, process development, and production problem solving. Contact him at 651/686-5400; jwalker@tjwa.com; tjwa.com.