Static Beat | Static Control for Films with Conductive Layers
- Published: February 27, 2018, By Kelly Robinson
Sparks from metallized webs and films with conducting traces are difficult to suppress because static control devices are ineffective.
Films with metallized layers or conductive traces are important because metallized layers provide excellent barrier properties. Conductive traces on insulating films enable electronic functionality. Some high value products, such as currencies and financial certificates, contain metallized security ribbons. The static problems on films with conductive layers in Table I are challenging because static control devices are ineffective in dissipating static on films with metallized layers or conductive traces.
Table I. Static Problems with metallized webs or with webs with conductive traces. |
|
1. Static sparks ignite fires when splices pass through solvent coaters. |
|
2. Sparks ignite fires when a tension loss allows a metallized web to drape across the pins of an active static bar. |
|
3. Sparks at the slit edges of films with buried metallized layer ignited fires. |
|
4. Cascading sparks occur between isolated metal traces running across the film. |
Historically, conductive layers have been designed into products to provide static protection. In 2004, the Academy of Motion Picture Arts and Sciences awarded a Scientific and Engineering Award (Academy Plaque or “Technical” Oscar Award) to my former colleagues Kenneth L. Tingler, Charles C. Anderson, Diane E. Kestner, and Brian A. Schell of the Eastman Kodak Co. for the successful development of process-surviving antistatic layers for motion picture films. These conductive layers are covered with insulating, polymeric layers that protect the antistatic layer from photographic processing liquids. This technology successfully controls the static charges that otherwise accumulate on films during high-speed printing operations.
While the buried, conductive layer in motion picture film provides excellent static protection, films with metallized layers or conductive traces for many other applications experience the static problems in Table I. Suppressing static sparks in these applications is difficult because static control devices are ineffective when dissipating static on webs with metallized layers or conducting traces.
Ground the conductive layer to suppress sparks on films with conductive layers. When the metallized layer is exposed, touching a metal idler roller grounds the conductive layer. However, when the conducting layer is laminated or coated with an insulator, the conducting layer never touches an idler roller. Any static charges on the conducting layer are trapped and can cause static problems.
I have tried many different ways to ground a conducting layer covered by an insulating layer. I have poked the film with a sharp, metal pin, slit the film with a metal slitter knife, and touched the slit edge with a metal brush. None of these techniques reliably grounds the covered, conducting layer.
The only reliable method to ground the covered, conductive layer in Figure 1 is to touch the exposed edges with metal idler rollers. For laminated films, design the product so that the width of the conducting layer WCONDUCTOR in Figure 1 is larger than the width of the laminated film WLAMINATE by at least 10 mm.
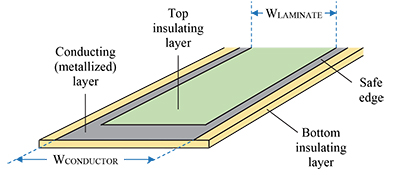
Similarly, for coated films, design the product so that the width of the conducting layer is larger than the width of the coated insulating layer by at least 10 mm. When the exposed metal edge or “safe edge” touches metal idler rollers, the conducting layer is grounded. Of course, safe edges are needed only for solvent coating operations or other sensitive operations where sparks would pose risks. Once these sensitive operations are finished, the safe edges may be trimmed.
Designing products with safe edges adds some “structural waste” to the value stream. However, safe edges are needed because they suppress static sparks. Static control devices that we normally use to suppress sparks are ineffective on webs with metallized layers or conducting traces. To see why, let’s take a look at how static dissipators work.
The static bar in Figure 2 generates equal numbers of positive and negative ions near the tips of the pins. The polymer web passing beneath the static bar carries negative static that induces an electric field to the nearest conducting object. Here, the nearest conducting object is the machine frame and the static bar. Positive ions from the static bar move along the electric field lines and deposit on the web neutralizing the negative charges.
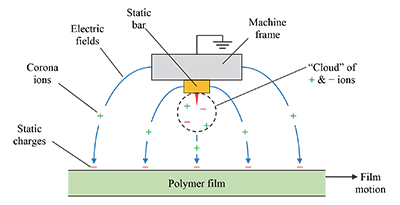
The negative static on the film in Figure 3 also induces an electric field to the nearest conductor. For films with metallized layers, the nearest conductor is the metallized layer. No electric fields extend from the static on the film to the static bar. Even though the static bar generates positive and negative ions, these ions remain near the pins. The static charges on the film remain unchanged as the metallized film passes beneath the static bar. The static bar cannot “see” the static on the film because the pins are farther from the static than the metallized layer.
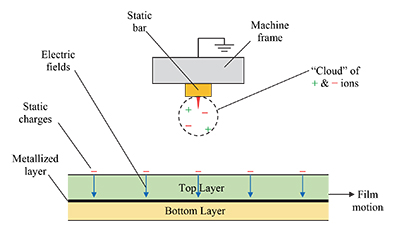
Metallized layers have many benefits including providing excellent barrier properties. Conducting traces on films enable electronic functionality and valuable security features. And, conductive layer can provide excellent static protection in some applications. Designing products to have “safe edges” for sensitive operations such as solvent coating grounds the conductive layers that suppresses sparks.
Feel free to contact me if you have any questions or if you would like additional information. My email address is Kelly.Robinson@ElectrostaticAnswers.com.
Static control expert Dr. Kelly Robinson, president of Electrostatic Answers, has 27+ years of experience in problem-solving and consulting. Kelly writes PFFC's Static Beat column and the Kelly on Static blog. Contact him at 585-425-8158; kelly.robinson@electrostaticanswers.com; www.electrostaticanswers.com.