Gravure Versus Flexo Printing-Part 1
- Published: July 01, 2009, By By David Argent Contributing Editor
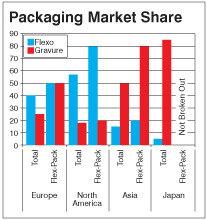
Gravure and flexo, two primary printing processes, continue to compete head to head in the packaging market segment. Both have strengths and weaknesses, and it is revealing to see there are different market share allocations, depending on where in the world the data is collected (see Figure 1).
Brand owners in Europe are said to have a perception of gravure as “simple, robust, and of high quality, and they allocate their flexo and gravure business on the basis of required quality. By contrast, in North America, flexo printing prevails and has met the quality requirements of the packaging industry.
Both gravure and flexo can meet the print requirements of the brand owners, so a look at the two technologies provides insight into what factors have been in effect, particularly in North America. History can be a good teacher.
Evolution of Flexo Printing | Some three decades ago flexo was capable of only basic designs due to many inherent press variables. It often was referred to as “rubber stamp” printing. In a 2002 presentation(Figure 2) by Windmoeller & Hoelscher Corp., this evolution was summarized as the result of several fundamental drivers that strengthened the appeal of flexo to packaging converters:

-
Flexo presses were simpler in design and cheaper than gravure presses with the same color capability.
-
Consumer marketing was changing from mass-marketing to more specific matching of product packaging to consumer characteristics, resulting in shorter runs, a trend that obviously favored flexo over gravure at that time.
-
Simultaneously, the continual improvement of flexo technology, at both the OEM and supplier level, made flexo more competitive.
-
There were also prepress issues with gravure in the '80s stemming from hazardous cylinder etching chemicals that extended cylinder engraving times and long press setup times. These factors hampered gravure in the growing trend of smaller orders and more frequent print runs.
-
During this period, truly innovative technological advances were adopted in every area of the flexo process. Most of all, the process became measurement based, data driven, and predictable — the rubber stamp image was gone forever.
-
Lastly, compared to gravure, the flexo movement was supported by an organized marketing effort spearheaded by organizations such as the Foundation of Flexographic Technical Assn. and technology leaders within the flexo industry.
- European Rotogravure Assn. http://www.era.eu.org/
- Gravure: Can It Fight Flexo? Gravure, August 2002
Process improvement expert David Argent has 30+ years of experience in process analysis with particular emphasis on ink and coating design and performance. Contact him at 314-409-4304; djvargent@sbcglobal.net.