Green Gravure
- Published: August 01, 2008, By By Edward Boyle, Contributing Editor
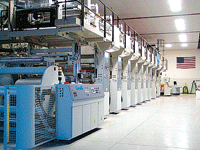
At a time when many flexographic printers and converters are focused on “growing green,” one New York-based converter of flexible packaging and labels is going one better: by going green — and gravure. Apple Converting installed a 47-in., nine-color Cerutti R960/2 gravure press nearly two years ago that runs at speeds to 1,000 fpm — and does so using water-based inks on as many runs as possible. The press offers Apple's customers a marked improvement in quality for those in the food and beverage, cosmetic, confectionary, consumer products, pharmaceutical, and medical device markets, while minimizing the use of solvent-based inks.
“Solvent inks and gravure typically go together,” explains Fred DiLorenzo, president. “But we've already had proven success with water-based inks. It's certainly not going to fit every gravure application, but we're looking to go in that direction.”
Seizing Opportunity
DiLorenzo notes that ink type was never an issue during Apple's first 25 years in business, since the company used ten flexographic presses that printed up to eight colors. When the company decided to add its eleventh press two years ago, it was faced with a decision: Install yet another familiar flexo press or enhance its technologies by going gravure. DiLorenzo says the choice was an easy one.
“New flexo presses are certainly getting much better in their technologies; they're faster and more efficient,” explains DiLorenzo. “But we said, ‘If we get another flexo press, we'd still have limitations. We may have more efficient runs and maybe faster speeds, but we still couldn't capture the gravure market.’ And there's a lot of business out there. When we looked at the numbers, we felt there was a lot more opportunity on the gravure side.
“Printing is printing,” DiLorenzo notes of the ease of implementing the new technology in what was previously an all-flexo house. “There are different methods to transfer ink to substrates; the basics are the same, but the technologies are different. Gravure is known for its high quality, consistency, long run lengths, and speed. It's certainly opened things up as far as our capacity, our capabilities, and our quality.”
DiLorenzo says Apple chose the Cerutti over other gravure press manufacturers because it enjoyed a reputation for quality that also proved a selling point to existing and potential customers.
“There were some options — some very good options — but Cerutti is very well respected throughout the world, and they've been around for many years,” notes DiLorenzo. “Anyone who's been around the gravure industry knows the Cerutti press, and it definitely makes a difference when we present it to customers.”
Defects Detected
A BST Pro Mark Premius digital 3Chip inspection system automatically performs high-resolution defect detection over the entire repeat area. The use of digital images and digital signal transmission technology results in a system insensitive to electronic noise and ambient light.
The system utilizes powerful algorithms that allow it to automatically detect a variety of common print defects such as streaks, hickeys, voids, spots, haze, misregister, missing type, and fill-in. Defect management software allows Apple to determine if and when a particular defect should be flagged or defined as acceptable or to select certain areas of the job for more or less comprehensive inspection.
“The system that we have on this press will monitor what is happening during the run and throughout the roll, so we can catch defects or variances on the fly and make adjustments as necessary,” explains DiLorenzo. “Without this type of system, you run the risk of producing out-of-spec rolls, which can be very costly. Time is lost as well.”
Due in part to the increased volume generated by its Cerutti press, Apple is currently planning to consolidate its two New York plants in Norwich and Oneonta — totally 90,000 sq ft — into a single Oneonta facility. The transition should be completed mid-year 2008.
In addition to its presses, that facility also will house seven slitter/rewinders that can accommodate 62-in. master rolls, as well as coaters and laminators. DiLorenzo expects to expand the current 50-person workforce as its Cerutti ultimately reaches 24-hr operation.
“We constantly strive to achieve total customer satisfaction,” explains DiLorenzo. “Every day is a challenge. We're not a huge company, but we are now catering to larger companies mainly because of the additional capacity and the quality of the gravure press.”
Supplier info
Cerutti Group | www.cerutti.it
PFFC-ASAP 304
BST Pro Mark | www.bstpromark.com
PFFC-ASAP 305
Contributing Editor Edward Boyle, based in Reading, PA, has covered the converting industry for more than 23 years. Contact him at EJB Communications; 610-670-4680; ejbcomm@aol.com.
Converter Info
Apple Converting Inc. | 176 Corporate Dr., Oneonta, NY 13820 | 607-432-6500 | www.appleconverting.com
Guiding the Press
In addition to providing Apple Converting with superior quality, the Cerutti gravure press is equipped with an Autotron Packaging 2600 register guidance system from Quadtech. The Autotron 2600 is designed for maximum quality, flexibility, and waste reduction.
It incorporates an expanded selection of miniature scanning heads and a “low-contrast lock-on” feature that enables the heads to work with very low-contrast marks encountered in the printing of packaging and decorative materials.
By installing the Autotron 2600 on the Cerutti press, Apple Converting VP Fred DiLorenzo says the company was able to make short work of once-difficult jobs such as printing pale colors and low-contrast varnishes on a challenging substrate. The company was able to further ensure accurate, single-mark register throughout the printing process.
Supplier Info
Quadtech | www.quadtechworld.com
PFFC-ASAP 306