Growth Strategy
- Published: June 01, 2009, By By Edward Boyle, Contributing Editor
In the midst of these uncertain economic times, even some successful companies are hesitant to make major capital purchases, fearing what tomorrow may or may not hold. But one flexible packaging converter has been busy purchasing equipment — and companies — to ensure its future is as bright as its past.
In the past two years, Ampac Flexibles has acquired converting operations across the country in Auburn (Seattle), WA, and around the world in Eberdingen, Germany. In the last four months of 2008, the company also installed new equipment at its facilities in Auburn and Elk Grove Village, IL.
“We're targeting some growth market niches,” explains Sal Pellingra, Ampac's innovation and marketing director. “And in other markets where we're entrenched, we're working to improve our product offering.”
With 15 manufacturing centers in North America and Asia, Ampac has grown “tenfold” to $300 million in annual sales in the past ten years, says Pellingra, both through acquisitions and growth in key market segments. Its product line includes stand-up pouches, high-end performance flexible packaging materials, and rollstock for the food, beverage, medical, pharmaceutical, and health and beauty aids markets, among others.
The company also provides more than 200 custom and proprietary film blends. They are designed to meet customers' specialty film packaging requirements.
In May 2007, Ampac greatly enhanced its market position with the acquisition of Mohawk Northern Plastics, a fully integrated flexible packaging converter in Auburn. Just four months later, Ampac purchased Floeter Flexible Packaging Group, with two manufacturing facilities in Germany and one in Chicago.
Then in December 2008, the company made capital investments at two US facilities, installing a new Windmoeller & Hoelscher extrusion system in its 270,000-sq-ft Auburn plant and a Totani pouchmaking machine in its 55,000-sq-ft Elk Grove Village facility.
Organic Growth
Installation of the 110-in. W&H Varex extruder has given Ampac's Auburn plant, which now converts 55 million pounds of film annually, the ability to increase the output and variety of innovative multilayer film structures. Ampac says the high-speed W&H line improves service to key target markets, including fresh and frozen foods, and provides quality sealant webs to the converting industry. Running speed is 1,500 pph.
“The primary reason [the equipment was installed in the suburban Seattle facility] is in alignment with Ampac's long-term capital investment plan. Ampac is focused on exceeding customer expectations in key markets. With the new line, Seattle is better positioned to service the growing fresh and frozen foods markets,” notes Pellingra. “It also allows Seattle to broaden their product offering in other key sealant and coextruded film markets. This is the first step of a capital growth plan for this key Ampac site.”
In addition to the new extruder, the plant houses 14 others, in widths from 36-110 in., from manufacturers that include Egan Davis-Standard and Gloucester. The plant also has three W&H printing presses — plus two from Carint and one from Paper Converting Machine Co. — with six to ten colors and widths from 13.75-60 in., plus three Stanford rewinders and other ancilliary equipment.
Page 2 of 2
Ampac's new extrusion line is part of the company's capital growth strategy and commitment to high quality packaging. In addition to the new line, Ampac worked with W&H to upgrade an existing extrusion system that was installed in 2004. “Ampac Flexibles is committed to meeting our customers' increasing requirements for high quality extrusion and flexible packaging at a price and delivery that keep them competitive in this quickly changing marketplace,” says Pellingra.
“Our new W&H line is the latest technology in blown film production, providing high film quality and outstanding ergonomics,” notes Dan McFarland, president of Ampac's Performance Printed Films group. “It also fits Ampac's sustainable goals with high efficiencies and short startup and changeover times, resulting in reduced material waste and higher productivity.”
Pouch Flexibility
Installation of the new 32-in. Totani Model BH-80HVLLLS-M pouchmaking machine has given Ampac's Elk Grove Village plant the ability to increase significantly the output of flexible pouches, including standard three-side seal, stand-up, and retort pouches. The high-speed Totani operates at 240 cycles/min, with laminate roll changes on the fly. The unit reportedly cuts pouches cleanly and precisely at very high speeds. It includes Totani's “Heat Pipe” technology, which provides high quality sealing and a stable cooling mechanism. Automatic adjustment functions “Photo Mark Sensor” and “Print Smooth” are designed to guarantee stable dimension accuracy.
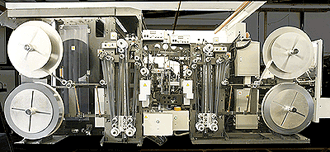
The Totani addresses the need for flexibility in the marketplace. “We are excited to have a machine with twice the output of comparable machines, especially with increased efficiency that doesn't compromise seal quality,” says Marc Rapp, president of Ampac's Global Pouching group. “We're pleased with the technology, advanced features, and the exceptional seal quality at high output speeds.”
Adds Pellingra, “The Totani allows us to offer a broad range of pouch styles, and the higher efficiencies — especially on roll changes and changeovers — are in keeping with Ampac's commitment to quality, reduced waste, and the environment.
“Each of our facilities has its own technical expertise where we've created a niche in the marketplace. We've been able to create a synergy by taking the best of each company and sharing that with the rest of the organization.”
Supplier Info
-
Windmoeller & Hoelscher Corp. | www.whcorp.com
PFFC-ASAP 330 -
Totani Corp. | www.totaniamerica.com
PFFC-ASAP 331 -
Egan Davis Standard | www.davis-standard.com
PFFC-ASAP 332 -
Gloucester Engineering | www.gloucesterengineering.com
PFFC-ASAP 333 -
Carint | www.carint.com
PFFC-ASAP 334 -
Paper Converting Machine Co. | www.pcmc.com
PFFC-ASAP 335 -
Stanford Products | www.stanfordproducts.com
PFFC-ASAP 336
Contributing Editor Edward Boyle, based in Reading, PA, has covered the converting industry for more than 24 years. Contact him at EJB Communications; 610-670-4680; ejbcomm@aol.com.
Converter Info
▶Ampac Packaging LLC | 12025 Tricon Rd., Cincinnati, OH 45246 | 513-671-1777 | www.ampaconline.com
Innovation Rewarded
Ampac Flexibles has been honored several times by the Flexible Packaging Assn. The company won a Silver Award for Technical Innovation in 2008 for its Wetbone “water-in-a-pouch” product for pets (see PFFC July 2007, p26). The bone-shaped resealable stand-up pouch features two compartments — a reservoir for enriched water at the bottom and a drinking bowl at the top. The design includes channels allowing water to fill the bowl and ensures unconsumed water returns to the reservoir. The pouch is a polyester/foil/linear low-density polyethylene lamination. In 2007, Ampac won a “highest achievement award” for its “Smart Pack” system, the first “pouch within a pouch” liquid yeast package for beer and wine making (see PFFC March 2007 p52). To activate the yeast, the inner packet containing the malt nutrient base is guided externally to the corner of the sealed retort pouch. When the inner seal is broken, the contents interact and begin metabolizing.