Pollution Control: 10 Tips To Cut CO2
- Published: September 01, 2010, By By Mike Scholz, Anguil Environmental Systems Inc.
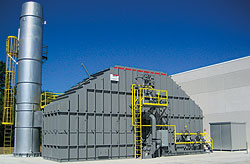
With mandatory greenhouse gas (GHG) reporting on the horizon, converters soon could be paying for the carbon emissions generated by some of their pollution control systems. Here are ten tips for reducing carbon emissions from your oxidizer.
-
Know how much your oxidizer is supposed to be costing you to operate | The “out of sight, out of mind” approach is entirely too prevalent these days when it comes to air pollution control equipment. With relatively minimal inputs, oxidizer vendors can run a performance model for you and give you the expected operating cost range for your oxidizer system.
-
Pay attention to the percentages | After five years of operation, a regenerative thermal oxidizer (RTO) originally designed for 95% TER (thermal energy recovery) may have slipped to 93%. This might not sound like a big deal, but an average-sized RTO (25,000 SCFM) operating for a full year at 93% TER versus 95% TER could cost upwards of an additional $65,000/yr.
-
Know your emission loading | Often it is peak VOC (volatile organic compound) loads that determine your oxidizer design but averages that determine your oxidizer operating cost. When an oxidizer is specified, designed, and installed, generally it is the anticipated VOC loading peaks that dictate the amount of heat recovery incorporated. After a few years of operation, it may be time to examine whether the design was too conservative and if the peak solvent usage is much lower than originally estimated. Operating an oxidizer designed to handle a theoretical peak loading may be costing you much more than necessary for your actual day-to-day production loading.
-
Know what oxidizer system would be specified for your process today | Finding out exactly what would be specified to treat your process exhaust today is a valuable exercise — especially if your existing equipment is in need of significant repairs or upgrades. Knowing what would be specified in today's energy-conscious market can save you from sinking too much money into an inefficient oxidizer system.
-
Know what grant money is available to you | Energy reduction upgrades to existing equipment will have an associated initial capital cost. This can be reduced significantly with grant money from local utility companies. Across the country, money has been earmarked for the specific purpose of funding energy reduction projects. Know what grant money is available to you, whom to contact, when and how to apply.
-
Concentrate high volume, low VOC airstreams prior to the oxidizer | If a significant portion of the air entering your oxidizer is at or near ambient temperature with low levels of VOC loading, a concentrator may be applicable for reducing the heat input required by your oxidizer. These systems take exhaust air at or near ambient temperatures and concentrate it so what actually is sent to the oxidizer is reduced by a factor of 8-15 times. This greatly reduced airflow is typically fuel-rich with VOCs and much less of an operating cost burden on the system.
-
Focus on combustion air | Combustion air, both in your oxidizer system or in your process burners, often is overlooked as a potential area for cost savings. These smaller fans, more often than not, are supplying fresh air at outdoor temperatures directly into the oxidation chamber, where it must be heated to full oxidation chamber temperature. At a temperature difference usually more than 1,400 deg F, it does not take much airflow over the course of a year to add up to significant operating cost dollars.
-
Improve primary heat recovery | Oxidizers typically are designed with some form of internal heat recovery. Usually the hot purified gases leaving the combustion chamber are used to preheat the incoming solvent-laden airstream. This is referred to as the primary heat recovery of an oxidizer system. Projects that improve the primary heat recovery often offer the quickest payback because they provide additional heat recovery at all times the oxidizer is in service.
-
Consider secondary heat recovery | If improving primary heat recovery is not cost effective — or oxidizer operating conditions do not allow it — secondary heat recovery may be the best option for conserving the heat input to an oxidizer system. Heat exchangers can be added to the exhaust stack of an existing oxidizer to capture excess stack heat in air, water, or even steam. There is a wide variety of low back-pressure designs that can be added to an oxidizer's stack without requiring a replacement of the oxidizer system fan.
-
Properly maintain existing systems | Finally, no matter how well an overall system is designed, it cannot continue to operate at a high efficiency level without proper maintenance. A handful of small inefficiencies in system operation can lead to a large operating cost bill over the course of a year. At today's energy prices, regular calibration of feedback instruments and control loops can pay for itself many times over.
Supplier Info
- Anguil Environmental Systems | www.anguil.com
Circle 301 or visit
www.freeproductinfo.net/pff
Mike Scholz is a senior application engineer at Anguil Environmental Systems. He has been involved in the design and installation of new oxidizer systems as well as upgrades to existing systems of all makes and models for the past ten years. He has a Mechanical Engineering degree from the Univ. of Wisconsin Madison and can be reached at 414-365-6400; mike.scholz@anguil.com.