Dissipating Static
- Published: October 01, 2009
Static becomes worse in the winter when the humidity decreases. What measurements are important to track static? Relative humidity (RH) is at the top of the list because static is a competition between two very different mechanisms: separation and dissipation.
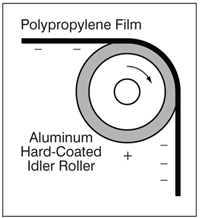
In Figure 1, PP film runs over a hard-coated aluminum idler roller. The film already has some negative charge because it has touched some rollers. When different materials touch and separate, one will have some positive charge, and the other will have negative charge. Using the triboelectric series as a guide, we know the film will have negative charge after contact with aluminum oxide in the hard coating. The film exits the roller with a third “?” sign, representing the charging by touching the roller.
The roller surface has one “+” charge that is equal and opposite to the charge deposited on the film. The charge on the roller surface dissipates or flows quickly to ground because there is an electrically conductive path from the roller surface through the bearings to the grounded machine frame.
One highly effective strategy for eliminating static problems is to coat the surface of the film with an electrically conductive layer. If this layer is sufficiently conductive, the negative charge on the film surface in Figure 1 could flow along back toward the roller and dissipate. Quaternary ammonium salts often are used for these antistatic coatings. The salt absorbs water from the air and dissociates forming mobile ions enabling current to flow. When humidity decreases, the antistatic layer absorbs less water, the number of ions decreases, and static performance degrades.
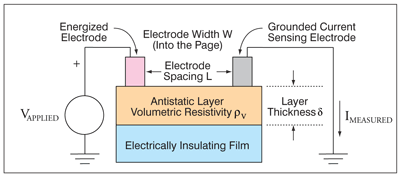
To specify an antistatic layer, we must define a measurement for this current flow and identify an acceptable range for our product. The appropriate measurement is surface electrical resistivity or surface resistivity as defined in ASTM D257 Standard Test Methods for DC Resistance or Conductance of Insulating Materials. The measurement method is illustrated in Figure 2.
The resistance (R) displayed by the megohmmeter is the applied voltage (Vapplied) divided by the measured current (Imeasured) as in Equation 1. The volumetic resistivity (ρv) is a material property of the coated layer. The units are indicated in brackets, and all distances are measured in meters.
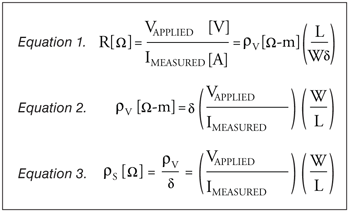
The measurement geometry affects current flow. When electrode spacing (L) increases, less current flows and resistance (R) increases. Similarly, when layer thickness (δ) or electrode width (W) increase, more current flows and resistance (R) decreases. Solving Equation 1 for ρv gives Equation 2.
Usually, the antistatic layer thickness (δ) is very small and difficult to measure. As a convenience, it often is grouped with volumetric resistivity, as in Equation 3, and given the name “surface resistivity” or “sheet resistivity” (ρs).
One source of confusion is that the units of surface resistivity are ohms, just like resistance. For clarity, we've adopted the units of ohms/square [Ω/ ] for surface resistivity. Notice that if the measurement geometry is square, that is, if W=L, the resistance displayed by the megohmmeter is the same as the surface resistivity, which is very convenient. Also, surface resistivity is a property of the coated layer and specifically not a material property. Coating a thicker layer of the same material will decrease surface resistivity.
For good static control, surface resistivity should be in the range 10+8 to 10+13 Ω/ depending on the process speed. The surface resistivity needs to be toward the lower end of this range for faster processes that run in excess of ~3,000 fpm (~100 mpm). Surface resistivities toward the upper end of this range are sufficient for slow processes running under ~30 fpm (~10 mpm). For a specific application, you'll have to run some trials to determine the surface resistivity specification for your product.
Static on film products is a competition between static charging and dissipation. The triboelectric series is a good guideline for static charging. For dissipation, surface resistivity is the key. For many antistatic materials, surface resistivity is a strong function of RH, making RH an important parameter. This is why static problems increase in the winter months.
Static control expert Dr. Kelly Robinson, president of Electrostatic Answers, has 27+ years of experience in problem-solving and consulting. Contact him at 585-425-8158; kelly.robinson@electrostaticanswers.com; www.electrostaticanswers.com.